液压系统执行机构经常出现的故障现象有系统压力正常执行元件无动作、执行元件动作太慢、机构爬行等几种形式。
这几种故障形式与流量异常密切相关,往往可以由流量这个工作参数查找故障原因并加以排除。本文详细分析液压系统执行元件3种故障现象的原因和消除方法。
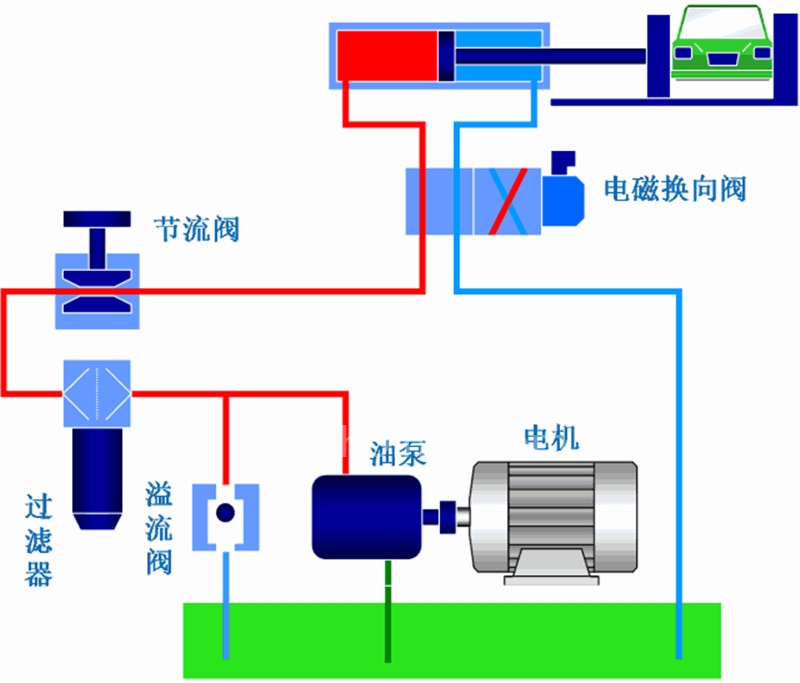
液压系统故障的特点:
1.隐蔽性:发生在系统内部,难以直接观测;
2.交错性:症状与原因之间交叉重叠,一个症状可能由多种原因引起,一个故障源可能引起多出症状;
3.随机性:电压,环境温度,工作任务的变化,污染侵入的随机性;
4.差异性:设计,加工材料及应用环境的差异,液压元件磨损劣化速度相差很大。
液压系统故障的原因:
1.设计原因
由于技术、工艺和经验等方面的原因,液压系统并非尽善尽美,选择的液压元件也不一定最合适,所以在分析故障原因时,首先考虑设计上是否存在问题。
2.制造原因
整套设备安装调试的过程中操作不当的话可能导致意想不到的故障出现。
3.使用原因
液压系统使用维护不当,不仅使设备故障频率增加。而且会降低设备的使用寿命。
4.维修原因
系统在维修中因为大拆大卸、不规范操作、随意调节、配件不配套等原因,会出现小故障修成大故障的现象。
表现一:执行元件动作太慢
原因1:內泄漏严重。
a.密封件破损严重。
消除方法:更换密封件。
b.油的粘度太低。
消除方法:更换适宜粘度的液压油。
c.油温过高。
消除方法:检查原因并消除。
原因2:外载荷过大。
a.设计错误,选用压力过低。
消除方法:核算后更换元件,调大工作压力。
b.工艺和使用错误,造成外载比预定值大。
消除方法:按设备规定值使用。
原因3:活塞移动时“别劲”。
1)加工精度差,缸筒孔锥度和圆度超差。
a.活塞杆与活塞不同轴。
消除方法:校正二者同轴度。
b.活塞杆全长或局部弯曲。
消除方法:校直活塞杆。
c.液压缸内孔直线性不良(鼓形锥度等)。
消除方法:镗磨修复,重配活塞。
d.缸内腐蚀、拉毛。
消除方法:轻微者修去锈蚀和毛刺,严重者必须镗磨。
2)装配质量差。
a.活塞、活塞杆与缸盖之间同轴度差。
消除方法:按要求重新装配。
b.液压缸与工作台平行度差。
消除方法:按要求重新装配。
c.活塞杆与导向套配合间隙过小。
消除方法:检查配合间隙,修刮导向套孔,达到要求的配合间隙。
3)液压缸端盖密封圈压得太紧或过松。
消除方法:调整密封圈,使它不紧不松,保证活塞杆能来回用手平稳地拉动而无泄漏。
4)双活塞杆两端螺母拧得太紧,使其同轴度不良。
消除方法:螺母不易拧得太紧,一般用手旋紧即可,以保持活塞杆处于自然状态。
原因4:脏物进入滑动部位。
a.油液过脏。
消除方法:过滤或更换油液。
b.防尘圈破损。
消除方法:更换防尘圈。
c.装配时未清洗干净或带入脏物。
消除方法:拆开清洗,装配时要注意清洁。
原因5:活塞在端部行程时速度急剧下降。
a.缓冲调节阀的节流口调节过小,在进入缓冲行程时,活塞可能停止或速度急剧下降。
消除方法:缓冲节流阀的开口度要调节适宜,并能起到缓冲作用。
b.固定式缓冲装置中节流孔直径过小。
消除方法:适当加大节流直径。
c.缸盖上固定式缓冲节流环与缓冲柱塞之间间隙过小。
消除方法:适当加大间隙。
表现二:机构爬行
液压缸运动速度在5mm/s以下时,应设法防止爬行现象产生。
原因1:新液压缸、修理后的液压缸或设备停机时间过长的液压缸,缸内有气或液压缸管道中排气未排净。
消除方法:空载大行程往复运动,直到把空气排完。
原因2:油缸内部形成负压,从外部吸入空气。
消除方法:先用油脂封住结合面和接头处,若吸空情况好转,则把紧固螺钉和接头拧紧。
原因3:从油缸到换向阀之间管道的容积比液压缸内容积大得多,液压缸工作时,这段管道内油液未排完,所以空气也很难排净。
消除方法:可在靠近液压缸的管道中最高处加排气阀,拧开排气阀,活塞杆在全行程情况下运动多次,把空气排完后再把排气阀关闭。
原因4:泵吸入空气。
a.油液中溶解一定量的空气,在工作过程中又生成气泡。
消除方法:在油箱内增设隔板,将回油经过隔板消泡后再吸入,油液中消泡剂。
b.回油涡流强烈生成泡沫。
消除方法:吸油管与回油管要隔开一定距离,回油管口要插入油面以下。
c.管道内或泵壳内存有空气。
消除方法:进行空载运转,排除空气。
d.吸油管浸入油面的深度不够。
消除方法:加长吸油管,往油箱中注油使其液面升高。